Gemini
Twins teams together in a single Project
Overview
Gemini is the third of the new generation of rockets developed for the European Rocketry Challenge in Portugal. Building upon the successes of its predecessors, Pyxis and Lynx, Gemini sets itself apart by introducing a new propulsive system:
Hybrid Engine “Furia”
allowing Skyward to compete for the first time ever in the ‘Hybrid SRAD 3000m’ category at EuRoC
specs
Cesaroni Pro98
FURIA
GLASS AND CARBON FIBER FUSELAGE
We decided to implement glass and carbon fibers fuselages. This allows us to find a perfect harmony with our own hybrid engine.
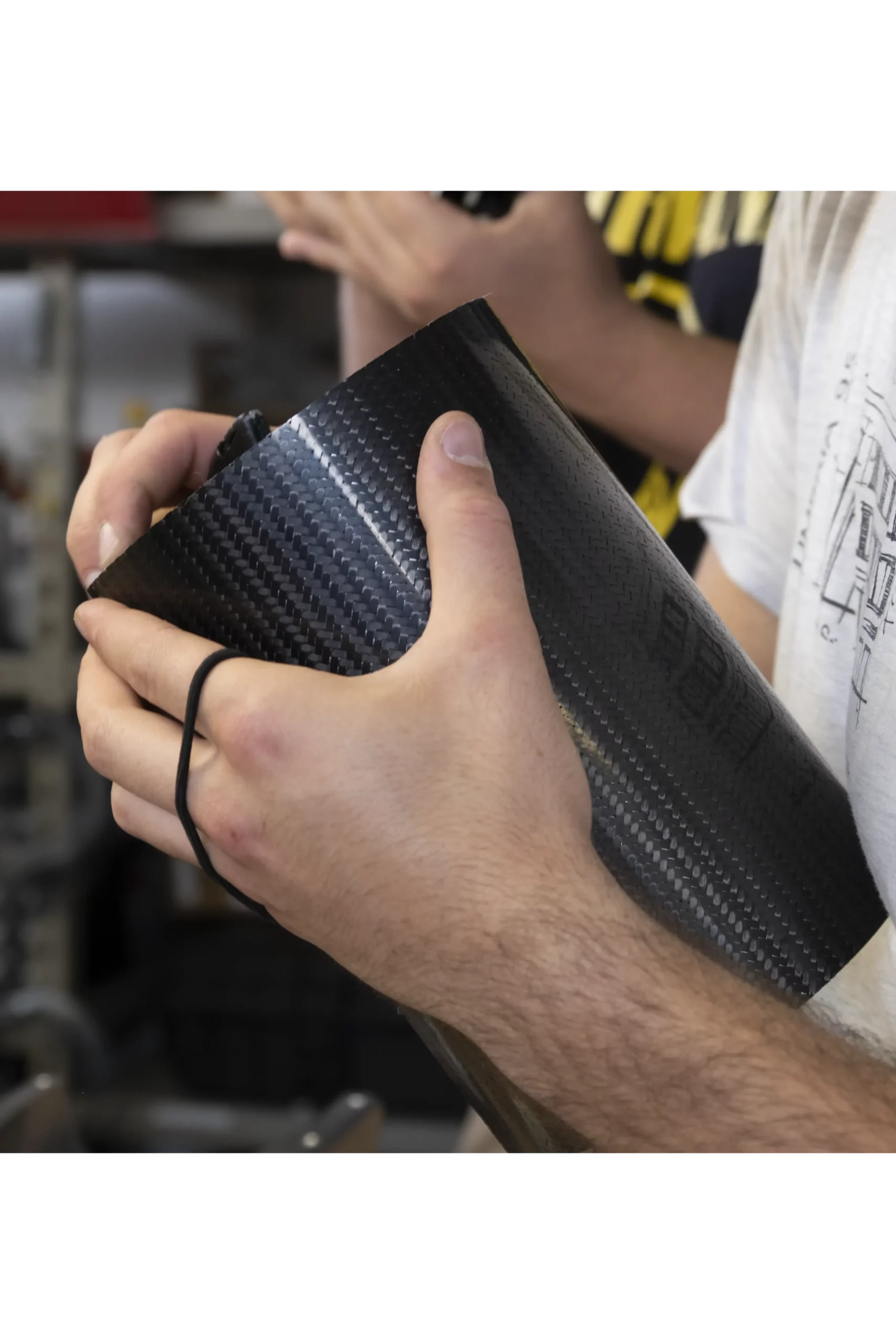
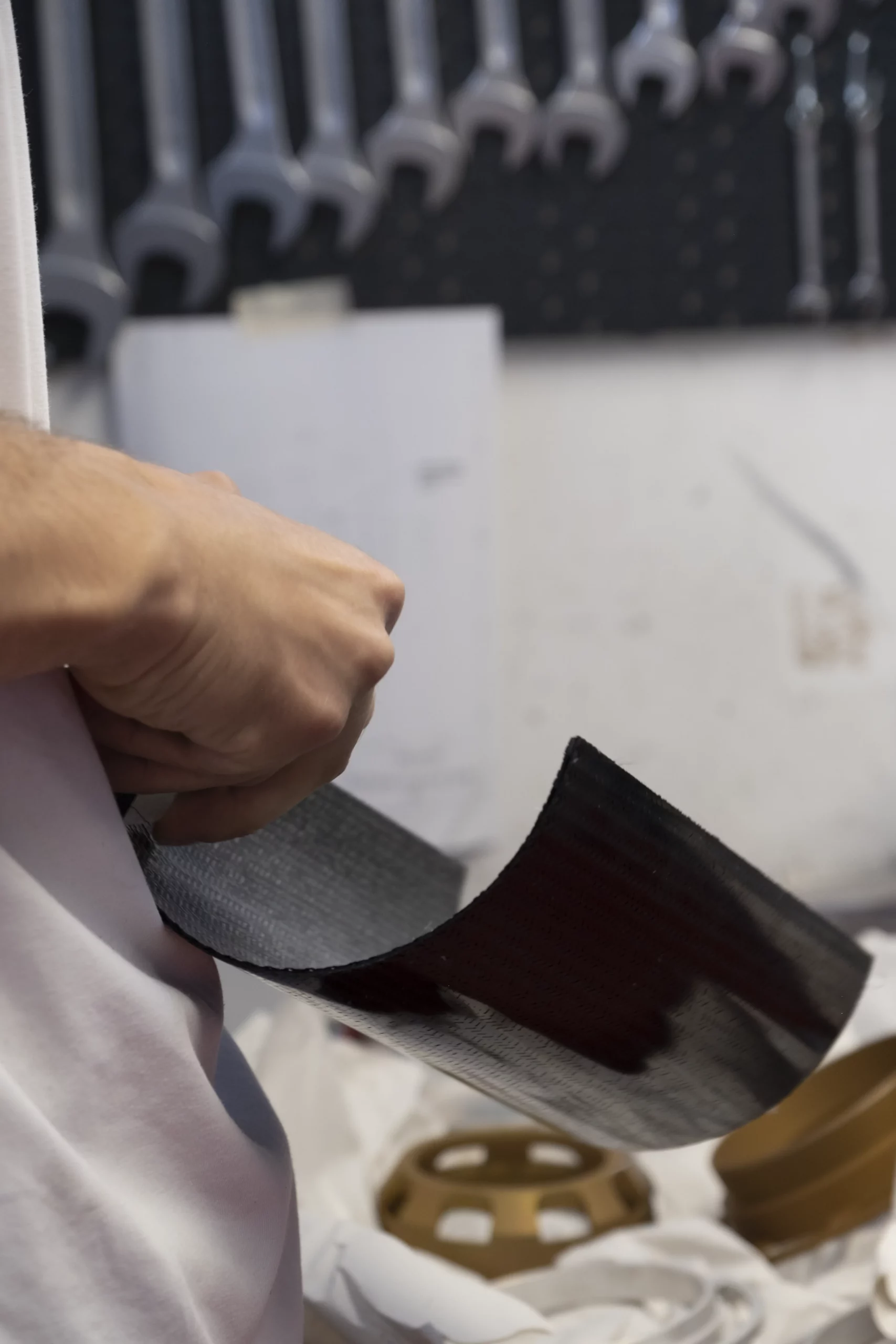
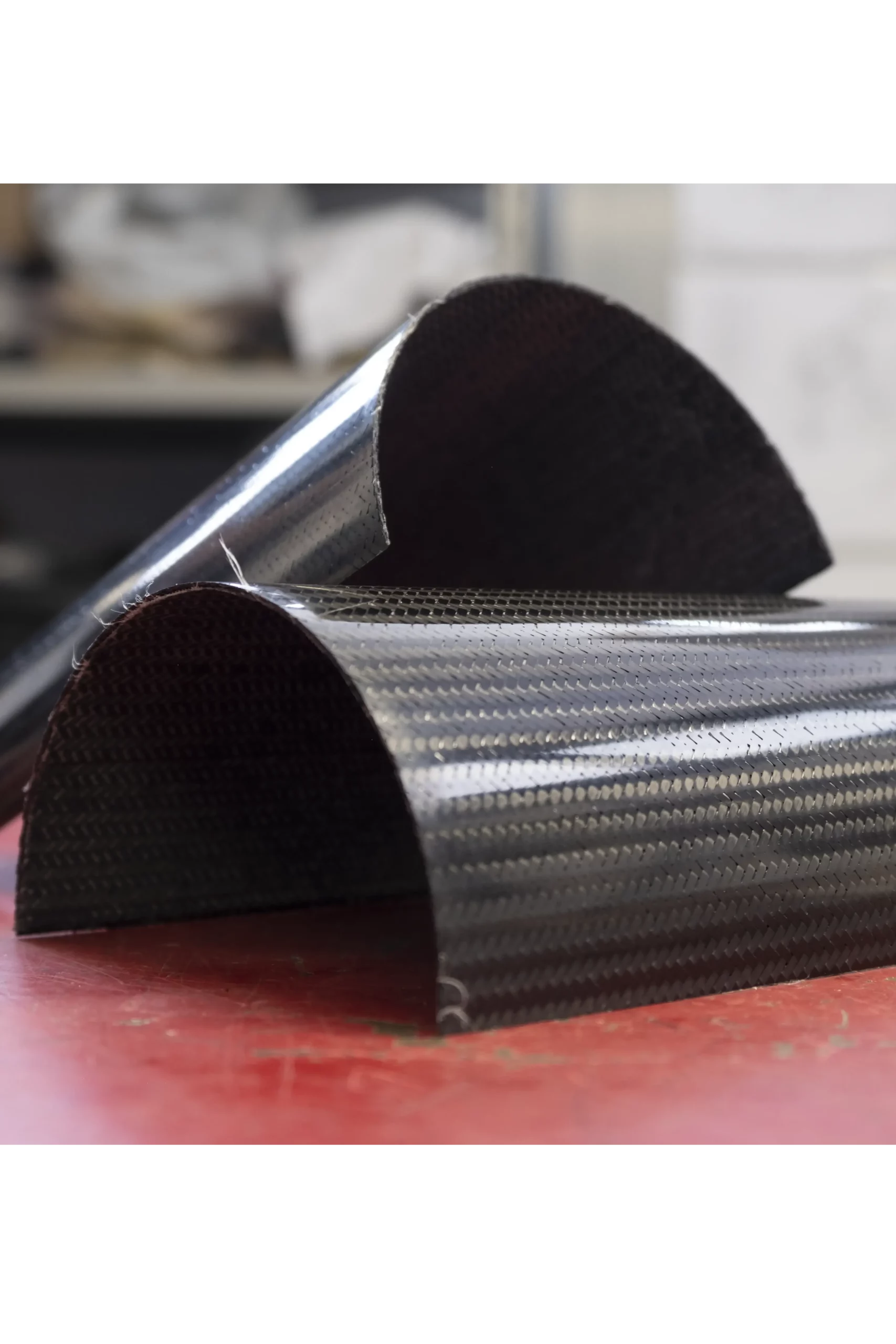
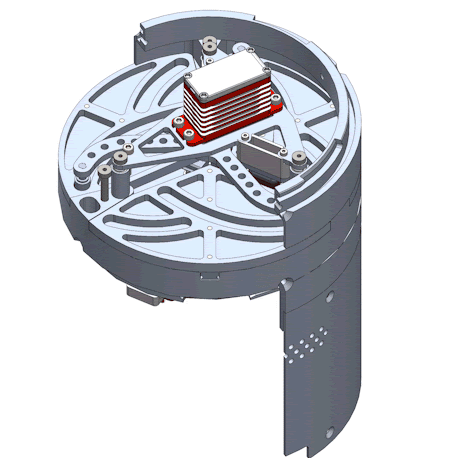
Air brakes
In order to precisely reach the target apogee of 3000m, Gemini uses an air brakes system to precisely control its speed.
During the flight, three aerodynamic surfaces are extented from inside the fuselage, controlled by a complex control algorithm that is capable of predicting how high the apogee will be, based on measurements from the onboard sensors, thus adjusting the trajectory of the rocket in real time.
Systems
Differently from the previous systems that are based on centralized systems, we want to introduce modular systems on Gemini.
Each board that made up the Deathstack, which, in previous projects, was the unique Electronics systems of reference, now is replaced with one or more boards that are smaller, easier to design and that solve determined tasks.
Every subsystem will be organized in a Motherboard, different from each subsystem, that collects all the daughter-boards needed to accomplish all the tasks required.
- Main motherboard:
The main electronics, situated in the Electronic Bay manages different tasks like communicate with the ground station telemetry and video signals after and before the lift-off, acquires and elaborate data through sensors, drive servomotors in order to adjust the altitude with air-brakes, detect the apogee and trigger the expulsion of parachutes. Due to the big amount of job requested to the whole subsystem, a decent number of daughter-boards are placed on the Main Mother-Board. - Engine Motherboard:
The engine electronics, placed between the tank and the combustion chamber, control the venting phase, the post-ignition and the engine shut-down. Everything is actuated by servo motors, and pressure sensors will be placed to monitor pressures on the tank. - Ground station Motherboard:
Ground Station main usage is to manage the communications between ground and rocket, in order to collect and analyze data directly from the base station.
Daughterboard
- Compute unit:
Is the brain in each System, holding the powerful stm32f767 and a 64MB DRAM - Radio Module:
the telemetry sent with 2 different frequency required 2 version of the radio module which share the same IC but a different Front end module, adapted to the 2 different frequency - GPS Module:
The board acquires gps’s datas acquired by thr module UBLOX NEO M8P. - Video Module:
A FPV drone video module is mounted on this board to send on-live video signal through the dedicated 5.8 GHz radio link recorded by cameras mounted on the rocket - Cutter/Actuator:
The main purpose of this board is to reliably power the cutter system through a strong current signal. - Sensor Board:
Thanks to the great amount of Analog and Digital Sensors, it’s possible to acquire every kind of data needed to Flight algorithm.
Parafoil
The Parafoil IPT designs, produces, and develops parafoil wing and software systems, safeguarding payloads and ensuring secure return to a specified point.
Our multidisciplinary team from various Skyward departments leverages diverse perspectives and expertise for optimal results.
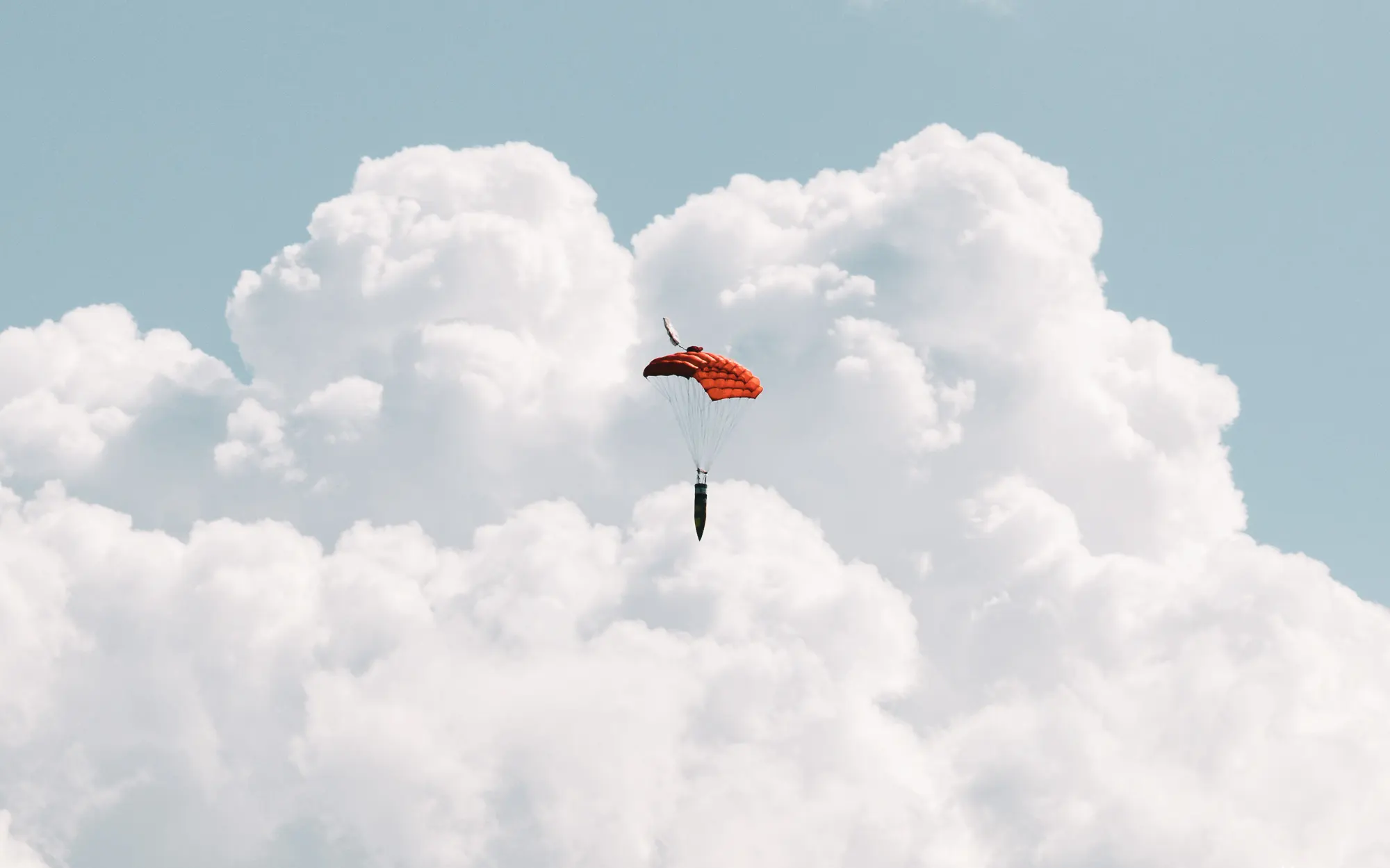
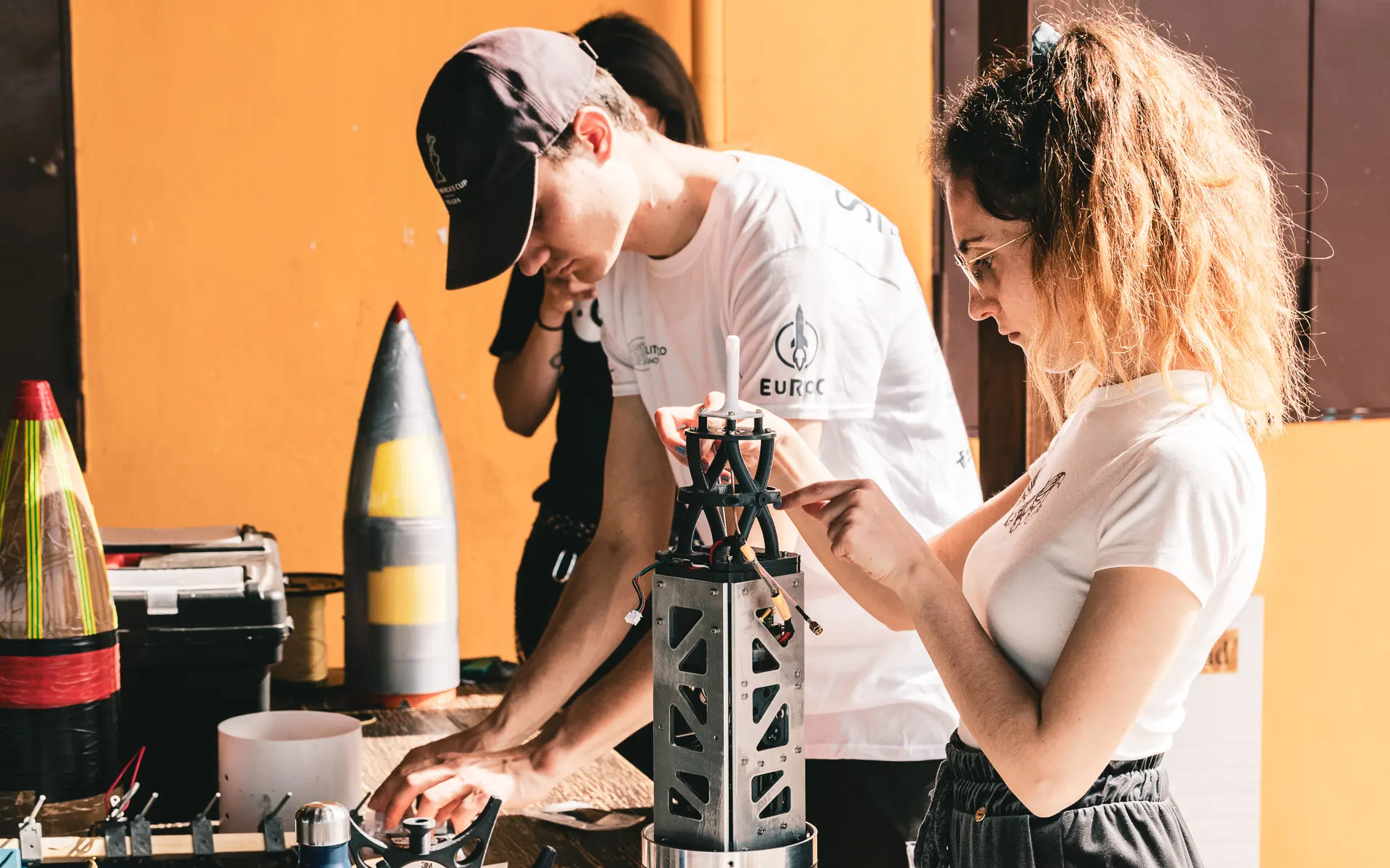
Furia
Propulsion System
Furia is propelled by 3D-printed ABS and self-pressurized N2O. Its pyrotechnic SRAD igniter is started by nichrome wire and is extensively tested to maximize reliability and repeatability.
The aluminum case is protected by phenolic-based insulating material, arranged in a configuration studied via finite element thermo-mechanical analyses, to resist the harsh environment.
The combustion chamber is optimized to reduce testing and integration time.
The oxidizer aluminum tank features threaded caps and is studied to grant safe landing and recovery
specs
Toroidal parachute
The most important element of the Gemini recovery system is the main parachute. Due to the bigger mass of this year rocket, a more efficient shape is selected, the toroidal canopy. This allows to keep the size of the parachute within reasonable limits.
The toroidal shape is a novelty in the field, so little data about it are available, and an intensive literature review, followed by a scaled down wind test campaign is performed to understand the best configuration of the canopy.
At the end of this process, a canopy of 7 m2 is sewn by the team. This will allow to bring Gemini to a successful recovery after its mission.
ENGINE OPTIMIZER
In order to design the most suitable engine according with the mission requirements, an optimization software has been created. It finds the optimal grain parameters, quantity of oxidizer and number of injection holes with the purpose of obtaining the best trade-off between engine mass, total length and velocity at launchpad exit.